تیرآهن چگونه تولید میشود ؟ مرحله اول در تولید تیرآهن، ذوب مواد اولیه است. این مواد اولیه شامل سنگ آهن، کک و سنگ آهک هستند که در کوره بلند ذوب شده و به آهن مذاب تبدیل میشوند.
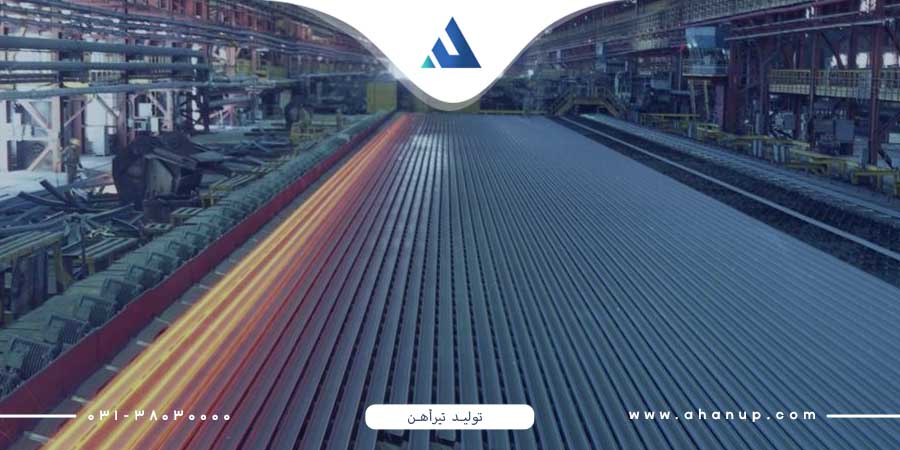
کک به عنوان سوخت در کوره بلند استفاده میشود و برای ایجاد گرمای لازم برای ذوب مواد اولیه ضروری است.سنگ آهک به عنوان شار در کوره بلند استفاده میشود و برای جدا کردن ناخالصی ها از آهن مذاب ضروری است.کوره بلند یک کوره عمودی است که برای ذوب مواد اولیه و تولید آهن مذاب استفاده میشود.در ادامه به بررسی اینکه تیرآهن چگونه تولید میشود در این مقاله از آهن آپ میپردازیم :
مراحل ذوب مواد اولیه
قبل از اینکه به موضوع اینکه تیرآهن چگونه تولید میشود باید بدانیم که تولید فولاد فرآیندی پیچیده و چند مرحلهای است که با آماده سازی مواد اولیه آغاز میشود. در این مرحله، سنگ آهن، کک و سنگ آهک به ابعاد مناسب خرد شده و به کوره بلند منتقل میشوند.
سپس، مواد اولیه به ترتیب خاصی در کوره بلند شارژ میشوند. سنگ آهن در بالای کوره، کک در وسط و سنگ آهک در پایین کوره قرار میگیرد. با گرم شدن کوره، مواد اولیه ذوب شده و به آهن مذاب تبدیل میشوند. کک به عنوان سوخت عمل میکند و گرمای لازم برای ذوب مواد را فراهم میکند.
آهن مذاب از کوره بلند خارج شده و در تصفیه کننده ها تصفیه میشود. ناخالصی های مانند گوگرد و فسفر با استفاده از مواد شیمیایی از آهن مذاب جدا میشوند.در نهایت، آهن مذاب تصفیه شده به شمش تبدیل میشود. شمش ها به عنوان مواد اولیه برای تولید محصولات فولادی مانند میلگرد، تیرآهن و ورق فولاد استفاده میشوند.
نکات مهم:
درون کوره بلند، دما به حدود 1500 درجه سانتی گراد میرسد. این گرمای شدید، مواد اولیه را ذوب کرده و به آهن مذاب تبدیل میکند. ظرفیت تولید کوره های بلند متفاوت است و می تواند تا چندین هزار تن آهن مذاب در روز باشد.فرآیند ذوب مواد اولیه در کوره بلند یک فرآیند پیچیده و پیوسته است. مواد اولیه به طور مداوم به کوره اضافه میشوند و آهن مذاب از پایین کوره خارج میشود. کیفیت آهن مذاب به کیفیت مواد اولیه و فرآیند ذوب بستگی دارد.
کیفیت آهن
علاوه بر کوره بلند، روش های دیگری برای ذوب مواد اولیه وجود دارد مانند:
- کوره قوس الکتریکی: در این روش از قوس الکتریکی برای ذوب مواد اولیه استفاده میشود.
- کوره القایی: در این روش از میدان الکتریکی برای ذوب مواد اولیه استفاده میشود.
انتخاب روش ذوب مواد اولیه به عوامل مختلفی مانند نوع مواد اولیه، ظرفیت تولید و کیفیت مورد نظر بستگی دارد.
تصفیه آهن در تولید تیرآهن
پس از ذوب مواد اولیه در کوره بلند، آهن مذاب به تصفیه کننده ها منتقل می شود تا ناخالصی های آن جدا شوند. ناخالصی های موجود در آهن مذاب می تواند شامل گوگرد، فسفر، سیلیسیم و منگنز باشد. این ناخالصی ها می توانند خواص مکانیکی و شیمیایی تیرآهن را به طور قابل توجهی کاهش دهند.
روش های مختلفی برای تصفیه آهن مذاب وجود دارد که عبارتند از:
• تصفیه با اکسیژن: در این روش، اکسیژن به آهن مذاب تزریق می شود تا با ناخالصی ها واکنش داده و آنها را به سرباره تبدیل کند. سرباره به دلیل چگالی کمتر از آهن مذاب، به سطح آن آمده و جدا می شود.
مثال: فرض کنید 100 تن آهن مذاب داریم که حاوی 1% گوگرد است. با تصفیه با اکسیژن، می توان 90% گوگرد را از آهن مذاب جدا کرد. به این ترتیب، مقدار گوگرد در آهن مذاب به 0.1% کاهش می یابد.
- تصفیه با گاز آرگون: در این روش، گاز آرگون به آهن مذاب تزریق می شود تا با ناخالصی ها واکنش داده و آنها را به نیتروژن و اکسید تبدیل کند. نیتروژن و اکسید به دلیل حلالیت کم در آهن، از آن جدا می شوند.
- مقایسه: تصفیه با گاز آرگون نسبت به تصفیه با اکسیژن، هزینه بیشتری دارد. اما تصفیه با گاز آرگون، کیفیت بالاتری را ارائه می دهد و می تواند ناخالصی های بیشتری را از آهن مذاب جدا کند.
- تصفیه با وکیوم: در این روش، آهن مذاب در خلاء قرار می گیرد تا ناخالصی های با نقطه جوش پایین مانند هیدروژن و نیتروژن از آن جدا شوند.
ریخته گری در تولید تیرآهن
پس از تصفیه، آهن مذاب به مرحله ریخته گری منتقل می شود. در این مرحله، آهن مذاب به شمش تبدیل می شود که به عنوان ماده اولیه در نورد گرم برای تولید تیرآهن استفاده می شود.
روش های مختلفی برای ریخته گری آهن مذاب وجود دارد که عبارتند از:
- ریخته گری ثقلی: در این روش، آهن مذاب به طور مستقیم در قالب ریخته می شود.
- ریخته گری پیوسته: در این روش، آهن مذاب به طور مداوم به قالب ریخته می شود و به صورت یک شمش پیوسته از قالب خارج می شود.
انتخاب روش ریخته گری به عوامل مختلفی مانند نوع محصول، ظرفیت تولید و کیفیت مورد نظر بستگی دارد.در ریخته گری تیرآهن، از روش ریخته گری پیوسته استفاده می شود. در این روش، آهن مذاب به طور مداوم به قالب ریخته می شود و به صورت یک شمش بلوم از قالب خارج می شود. شمش بلوم سپس به نورد گرم منتقل می شود تا به تیرآهن تبدیل شود.
مراحل ریخته گری پیوسته
در تولید شمش بلوم، ابتدا قالب از جنس مس یا فولاد گرم میشود تا از انجماد سریع آهن مذاب جلوگیری شود. سپس آهن مذاب به طور مداوم به قالب ریخته و در آن خنک شده و به جامد تبدیل میشود. در نهایت، شمش بلوم از قالب خارج و به طولهای مورد نظر برش داده میشود.
نکات مهم:
کیفیت شمش بلوم در کیفیت تیرآهن نهایی تاثیرگذار است. عواملی مانند سرعت ریخته گری و دمای آهن مذاب در کیفیت شمش بلوم تولیدی نقش دارند.سرعت ریخته گری بالا می تواند منجر به ایجاد ترک و حفره در شمش بلوم شود. این عیوب می تواند در تیرآهن نهایی نیز ظاهر شده و کیفیت آن را کاهش دهد.
دمای آهن مذاب باید به گونه ای باشد که از انجماد زودهنگام آن در قالب جلوگیری شود. انجماد زودهنگام می تواند منجر به ایجاد ترک و ناهمواری در سطح شمش بلوم شود.وجود ترک و حفره در شمش بلوم می تواند منجر به ایجاد عیوب در تیرآهن نهایی مانند ترک، ناهمواری، و کاهش استحکام شود.
تکنولوژی نورد با ابعاد آزاد و بسیار کارآمد
پس از ریخته گری، شمش بلوم به نورد گرم منتقل می شود تا به تیرآهن تبدیل شود. در نورد گرم، شمش بلوم با عبور از غلطک های متعدد، فشرده شده و به شکل تیرآهن در می آید.
مراحل نورد گرم
تولید تیرآهن فرآیندی شامل چند مرحله است که با گرمایش شمش بلوم آغاز میشود. شمش بلوم در کورههای گرم تا دمای حدود 1200 درجه سانتیگراد گرم میشود تا نرم و انعطافپذیر شده و برای نورد آماده شود.
در مرحله بعد، شمش بلوم گرم شده از غلطکهای متعدد عبور میکند. با عبور از هر غلتک، ضخامت شمش کاهش مییابد و عرض آن افزایش مییابد. این فرآیند نورد نامیده میشود و تا زمانی ادامه مییابد که شمش به شکل تیرآهن در آید.پس از نورد، تیرآهن نورد شده در هوا خنک میشود. در طی فرآیند خنک شدن، تیرآهن به طور تدریجی استحکام خود را به دست میآورد.در نهایت، تیرآهنها به طولهای مورد نظر برش داده میشوند. سپس تیرآهنها بستهبندی شده و برای مصارف مختلف برای شرکت بازرگانی آهن آپ ارسال میشود.
برای تولید تیرآهن با کیفیت، باید به سه عامل کلیدی توجه کرد:
- دمای نورد: باید طوری تنظیم شود که از ایجاد ترک و حفره در تیرآهن جلوگیری شود. دمای خیلی بالا، تیرآهن را ذوب یا ترک میدهد و دمای خیلی پایین، آن را ناقص نوردیده و شکننده میکند.
- سرعت نورد: سرعت بالا میتواند تنشهای داخلی در تیرآهن ایجاد کند که در درازمدت منجر به خم شدن، تاب برداشتن و حتی شکستن آن میشود.
- کیفیت غلطکها: غلطکها باید صاف و بدون عیب باشند تا سطح تیرآهن صاف و عاری از نقص باشد. عیوب غلطکها روی سطح تیرآهن نقش میبندند و کیفیت آن را پایین میآورند.
توجه به این سه عامل در کنار استفاده از مواد اولیه مرغوب و تجهیزات مناسب، کلید تولید تیرآهن با کیفیت بالا است.
برش و سایزینگ تیرآهن
پس از نورد گرم، تیرآهن ها به طول های مورد نظر برش داده شده و در سایزهای مختلف تولید می شوند. این فرآیند برش و سایزینگ، به دو روش کلی انجام می شود:
1. برش سرد:
- برش با اره نواری: این روش برای برش تیرآهن های با ضخامت بالا مناسب است.
- برش با فرز: این روش برای برش تیرآهن های با ضخامت کم مناسب است.
- برش با لیزر: این روش برای برش دقیق و ظریف تیرآهن ها مناسب است.
2. برش گرم:
- برش با قوس الکتریکی: این روش برای برش تیرآهن های ضخیم و سنگین مناسب است.
- برش با شعله: این روش برای برش تیرآهن های با ضخامت کم و متوسط مناسب است.
انتخاب روش برش به عوامل مختلفی مانند نوع تیرآهن، ضخامت تیرآهن، دقت برش و هزینه برش بستگی دارد.پس از برش، تیرآهن ها در سایزهای مختلف دسته بندی می شوند. سایز تیرآهن بر اساس ضخامت جان و بال تیرآهن تعیین می شود. رایج ترین سایزهای تیرآهن شامل تیرآهن IPE، تیرآهن INP، تیرآهن HEA و تیرآهن HEB می باشد.
سایزینگ تیرآهن به منظور ایجاد تنوع در محصولات و پاسخگویی به نیازهای مختلف در صنعت ساخت و ساز انجام می شود.
نکات مهم در برش و سایزینگ تیرآهن
کیفیت برش در صحت و سلامت تیرآهن نهایی آهن آپ تاثیرگذار است. برش باید دقیق و بدون عیب باشد.همچنین سایز تیرآهن آهن آپ باید متناسب با نیاز پروژه باشد. استفاده از تیرآهن با سایز نامناسب می تواند منجر به افزایش هزینه ها و کاهش ایمنی سازه شود.رعایت نکات ایمنی در هنگام برش و سایزینگ تیرآهن ضروری است.
نورد افقی باقابلیت تنظیم طول غلتک در تیرآهن
پس از نورد عمودی و قبل از خنک شدن نهایی تیرآهن، از نورد افقی برای تنظیم دقیق ارتفاع جان تیرآهن استفاده میشود. در این روش، غلطکهای افقی با قابلیت تنظیم طول، تیرآهن را در جهت افقی فشرده میکنند و ارتفاع جان آن را به طور دقیق تنظیم میکنند.
مزایای نورد افقی باقابلیت تنظیم طول غلتک
نورد افقی تیرآهن سایت آهن آپ مزایای متعددی دارد که در ادامه به چهار مورد از مهمترین آنها اشاره میکنیم:
1. تنظیم دقیق ارتفاع جان:
این روش امکان تنظیم ارتفاع جان تیرآهن با دقت بالا را فراهم میکند. به این ترتیب، میتوان تیرآهنهایی با ارتفاع جان دقیق و مطابق با نیازهای مختلف تولید کرد. این امر در صنعت ساخت و ساز و طراحی سازهها از اهمیت بالایی برخوردار است.
2. افزایش استحکام خمشی:
نورد افقی با افزایش ضخامت جان تیرآهن، استحکام خمشی آن را نیز افزایش میدهد. تیرآهن با استحکام خمشی بالا، در برابر بارهای خمشی مقاومتر بوده و میتواند در سازههای بزرگ و پلها مورد استفاده قرار گیرد.
3. کاهش تنشهای داخلی:
تنظیم طول غلطکها به طور متقارن، تنشهای داخلی تیرآهن را در طول جان آن به طور یکنواخت توزیع میکند. این امر از ایجاد تنشهای نقطهای و تمرکز تنش که میتواند منجر به شکست تیرآهن شود، جلوگیری میکند.
4. افزایش کیفیت سطح:
نورد افقی با صاف کردن سطح جان تیرآهن، کیفیت سطح آن را نیز افزایش میدهد. این امر باعث میشود که تیرآهن ظاهر زیباتری داشته باشد و برای مصارف ظاهری نیز مناسب باشد.
علاوه بر این مزایا، نورد افقی میتواند سرعت تولید تیرآهن را نیز افزایش دهد و هزینههای تولید را به طور قابل توجهی کاهش دهد.
مراحل نورد افقی باقابلیت تنظیم طول غلتک
1. پیش گرمایش:
قبل از نورد افقی، تیرآهن از مجموعهای از غلطکهای پیش گرم عبور میکند تا دمای آن به حدود 1000 درجه سانتیگراد برسد. این فرآیند مزایای زیر را به همراه دارد:
• افزایش انعطافپذیری تیرآهن آهن آپ: گرم شدن تیرآهن باعث میشود که انعطافپذیری آن افزایش یابد و در برابر تغییر شکل مقاومتر شود. این امر نورد تیرآهن را با سهولت و دقت بیشتر امکانپذیر میکند.
• کاهش احتمال ترک خوردگی: گرم شدن تیرآهن تنشهای داخلی آن را کاهش میدهد و احتمال ترک خوردگی در حین نورد را به حداقل میرساند.
• یکنواختی دما: عبور تیرآهن از غلطکهای پیش گرم، دمای آن را در تمام نقاط به طور یکنواخت افزایش میدهد. این امر کیفیت نورد را به طور قابل توجهی ارتقا میدهد.
2. تنظیم طول غلتکها:
پس از گرم شدن، تیرآهن به قفسه نورد افقی منتقل میشود. در این قفسه، مجموعهای از غلطکهای افقی با طولهای مختلف وجود دارد. طول غلطکها با توجه به ارتفاع جان مورد نظر برای تیرآهن تنظیم میشود. به طور کلی، هرچه طول غلطکها بیشتر باشد، ارتفاع جان تیرآهن بیشتر خواهد بود.
3. نورد و شکلدهی:
تیرآهن گرم شده از بین غلطکهای افقی عبور میکند و تحت فشار جانبی قرار میگیرد. این فشار توسط سیستم هیدرولیکی قدرتمندی اعمال میشود و باعث میشود که بالهای تیرآهن به سمت داخل خم شده و ارتفاع جان تیرآهن افزایش یابد. زاویه و فاصله غلطکها نیز در شکلدهی نهایی تیرآهن نقش دارند.
4. خنک شدن:
پس از نورد افقی، تیرآهن به محل خنککاری منتقل میشود. در این محل، تیرآهن به طور آهسته و تدریجی در هوا خنک میشود. خنک شدن تدریجی باعث افزایش استحکام تیرآهن و جلوگیری از ایجاد ترک در آن میشود.
نکات مهم:
- تنظیم دقیق طول غلتکها برای دستیابی به ارتفاع جان مورد نظر ضروری است.
- سرعت نورد و دمای تیرآهن باید به طور دقیق کنترل شود تا از ایجاد ترک و حفره در تیرآهن جلوگیری شود.
- غلطکها باید به طور منظم صاف و صیقلی شوند تا از ایجاد عیوب سطحی در تیرآهن جلوگیری شود.
- نورد افقی باقابلیت تنظیم طول غلتک در تولید تیرآهنهای با جان بلند و تیرآهنهای با مقاطع خاص کاربرد دارد.
مزایای نورد لبه دهنده با سایز دلخواه
تولید تیرآهن با سایزهای مختلف: این روش امکان تولید تیرآهن با عرض بالها و ضخامت جان دلخواه را فراهم میکند.
- افزایش استحکام تیرآهن: نورد لبه دهنده با افزایش ضخامت جان و بالهای تیرآهن، استحکام آن را نیز افزایش میدهد.
- بهبود کیفیت سطح تیرآهن: نورد لبه دهنده با صاف کردن سطح بالها و جان تیرآهن، کیفیت سطح آن را نیز افزایش میدهد.
- کاهش ضایعات: با استفاده از نورد لبه دهنده، ضایعات تولید تیرآهن به طور قابل توجهی کاهش مییابد.
- کاربرد : نورد لبه دهنده در تولید تیرآهنهای با سایزهای خاص، تیرآهنهای با بالهای پهن و تیرآهنهای با جان ضخیم کاربرد دارد.
نکات مهم:
- تنظیم دقیق غلطکهای لبه دهنده برای دستیابی به سایز دلخواه ضروری است.
- سرعت نورد و دمای تیرآهن باید به طور دقیق کنترل شود تا از ایجاد ترک و حفره در تیرآهن جلوگیری شود.
- غلطکها باید به طور منظم صاف و صیقلی شوند تا از ایجاد عیوب سطحی در تیرآهن جلوگیری شود.