همه چیز درباره رزین پلی استر و رزین وینیل استر
اگر میخواهید همه چیز درباره رزین پلی استر و رزین وینیل استر و الیاف شیشه را بدانید با ما در این مقاله همراه باشید!
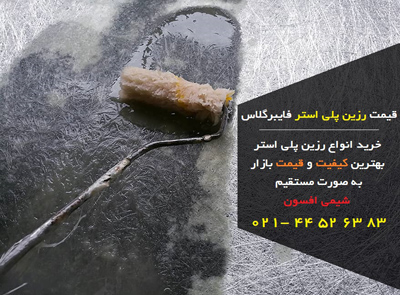
پلی استر:
به طیف گسترده ای از پلیمرها که در ساختار خود گروه شیمیایی استری -–COO داشته باشند نام پلی استر اطلاق می شود. پلی استرها از واکنش یک یا چند الکل دو یا چند عاملی با یک یا چند اسید دو یا چند عاملی ساخته می شوند که با توجه به ساختار و مواد اولیه تشکیل دهنده، این پلیمرها به دو دسته اشباع و غیر اشباع تقسیم بندی می شوند. صرفا پلیمر پلی استر غیر اشباع قبلیت استفاده در کاربری رزین را دارد.
پلی استر غیر اشباع (رزین پلی استر)
پلی استر غیر اشباع در فرمول نهایی خود دارای تعدادی پیوند دو گانه کربن- کربن می باشد که این پیوند دو گانه مستعد پیوندهای کراس لینک و ایجاد شبکه سه بعدی گسترده می باشد. در صورتی که در تولید پلیمر پلی استر از اسیدهای غیر اشباع استفاده گردد، محصول نهایی نیز ساختار پلی استر غیر اشباع دارد و قابل استفاده در کاربری رزین می باشد.
توجه: لازم به ذکر می باشد که پلیمر پلی استر گرما نرم مانند الیاف کربن در ساخت ظروف پلاستیکی و پارچه های مصنوعی کاربرد دارد و نیز پلی استر ترموست اشباع نیز در صنایع رنگ و پوشش های سطحی کاربرد دارد و صرفا پلیمر پلی استر غیر اشباع قابلیت شبکه ای شدن (کراس لینک) دارد و قابل استفاده به عنوان رزین در صنعت کامپوزیت می باشد.
فرمول ساخت رزین پلی استر غیر اشباع:
رزین پلی استر غیر اشباع = مونومر+ الکل (گلایکل ها) + اسید اشباع + اسید غیر اشباع
اسید غیر اشباع: دو نوع اسید غیراشباع مالئیک انیدرید و فوماریک اسید از متداول ترین اسیدهای غیر اشباع قابل استفاده در تولید رزین پلی استر می باشند.
الکل دو عاملی (گلایکل ها): این مواد در ساختار خود دارای دو گروه هیدروکسیل می باشند. متداول ترین گلایکل مصرفی در صنعت رزین پلی استر، پروپیلن گلایکل می باشد.
اسید اشباع: افزودن آن باعث کاهش تردی رزین و افزایش انعطاف پذیری می گردد. در میان اسید های اشباع استفاده شده در رزین، اورتو فتالیک اسید و ایزو فتالیک اسید متداول تر می باشند که به ترتیب به رزین نهایی تولید شده پلی استر غیر اشباع اورتو (Ortho) و ایزو (Iso) گفته می شود. رزین ایزو مقاومت مکانیکی، حرارتی و شیمیایی مطلوب تری دارد و به طور تقریبی در حدود 10 درصد قیمت آن نیز بالاتر از رزین اورتو می باشد.
مونومر: جهت تسریع و تسهیل در پخت پلی استر، کاهش غلظت رزین و سهولت استفاده رزین از مونومر استفاده می گردد. متداول ترین مونومر استفاده شده در رزین پلی استر، استایرن می باشد که بوی رزین ناشی از بوی استایرن است. 30 الی 50 درصد وزنی رزین پلی استر از استایرن تشکیل شده است. با اضافه شدن مونومر استایرن امکان شروع حداقلی واکنش و ژل شدن رزین پلی استر می باشد که جهت جلوگیری از ژل شدن ناخواسته در حین تولید و استفاده رزین، در حدود 0.2 درصد ممانعت کننده (کاهنده) از نوع هیدروکیتون (HQ) یا تولوهیدروکیتون (THQ) به رزین افزوده می شود.
دسته بندی رزین های پلی استر بر اساس ساختار شیمیایی
با تغییر در هریک از 4 ماده تشکیل دهنده رزین پلی استر، ساخت رزینی خاص امکان پذیر می باشد که هر یک از شرکت های تولید کننده رزین، با توجه به امکانات خود، چندین نوع رزین پلی استر مختلف را تولید می نمایند. تعدادی از انواع خاص رزین های پلی استر موجود در بازار، در ادامه ذکر شده است: (کاتالیزرها و شتاب دهنده مورد استفاده در انواع رزین های پلی استر همانند یکدیگر می باشند)
اورتوفتالیک: متداول ترین و کاربری عمومی
ایزوفتالیک: مقاومت شیمیایی، مکانیکی، حرارتی بالاتر از اورتو
ایزوفتالیک بر پایه NPG: مقاومت شیمیایی بالاتر از ایزوفتالیک معمولی
ترفتالیک: مقاومت حرارتی بالا
بیس فنل A (فومارات BPA): مقاوم در برابر محیط قلیایی و خورندگی
هالوژنه: مقاومت حرارتی بالا و مقاوم در برابر خورندگی
دسته بندی رزین های پلی استر بر اساس کاربرد و خواص:
رزین با کاربری معمولی: متداول ترین و پرکاربرد ترین رزین های مورد مصرف می باشند که رزین های پلی استر اورتوفتالیک در این دسته قرار می گیرند (محدوده ویسکوزیته cps 4000-500)
رزین های مقاوم در برابرآتش: با اضافه کردن انواع افزودنی های موثر در آتش، همانند آلومینیوم تری هیدرات (ATH)، می توان خاصیت خود خاموش شوندگی به رزین های پلی استر بخشید. در صورتی که استاندارد های بالای مقاومت در برابر آتش قطعات کامپوزیتی نیاز باشد با اضافه کردن مواد هالوژنه (تتراکلرو فتالیک انیدرید و کلرواندیک انیدرید HET) به رزین پلی استر، امکان دستیابی به رزین های ضد آتش مقدور می باشد، که در اصطلاح به رزین پلی استرهالوژنه معروف می باشد.
رزین های مقاوم در برابر حرارت: این نوع رزین با عدد بالای پارامتر HDT (دمای تغییر شکل حرارتی) شناخته می شود.
رزین های مقاوم در برابر مواد شیمیایی: اولین راه حل جهت افزایش مقاومت شیمیایی، افزایش ساختار شبکه ای در رزین پلی استر می باشد که این امر با افزایش دما و زمان پخت (post cure) امکان پذیر می باشد. علاوه بر روش ذکر شده، با تغییرات در مواد اولیه، دستیابی به مقاومت شبمبایی بالا و بهبود خورندگی رزین نیز امکان پذیر می باشد که از آن جمله می توان استفاده از الکل دو عاملی نئوپنتیل گلایکل (NPG )، اسید HET و بیس فنل A را ذکر نمود.
رزین مقاوم در برابر ضربه: ابن نوع رزین دارای چقرمگی بالا و تا حدی دارای انعطاف می باشد. (رزین های پلی استر ایزوفتالیک در مقابل ضربه مقاومت مناسبی دارند)
رزین های منعطف: هر چه انعطاف و ازدباد طول در نقطه شکست بیشتر باشد، میزان سختی سطح و استحکام قطعه کامپوزیت کاسته و میزان ضربه پذیری آن افزوده می شود و با اضافه کردن اسید های اشباع همانند اسید آدیپیک با اسید سباسیک به رزین، میزان انعطاف رزین پلی استر بهبود می آید.
رزین با جمع شدگی کم (Low profile resin): میزان جمع شدگی رزین های پلی استر غیر اشباع بعد از پخت در حدود 4 تا 10 درصد می باشد، این میزان جمع شدگی باعث کاهش دقت ابعادی، کاهش کیفیت سطح و ایجاد ترک های ریز در قطعه می گردد. جهت برطرف نمودن این مشکل، افزودن 10 الی 30 درصدی یک پلیمر گرمانرم همانند پلی اتیلن، پلی استایرن، اکریلیک و…به رزین پلی استر پیشنهاد می گردد.
رزین های مقاوم در برابر نور فرابنفش: پیوندهای دو گانه موجود در رزین های پلی استر، در مقابل نور خورشید (فرابنفش) جزو نقاط ضعف محسوب می شوند و باعث تغییر رنگ قطعه کامپوزیتی در دراز مدت می گردند. جهت بر طرف نمودن این مشکل، افزودن مواد پایدار کننده (جاذب) نور فرابنفش به میزان درصد پیشنهاد شده شرکت سازنده، قبل از ساخت قطعه پیشنهاد می شود.
رزین های سطحی کاربرد رزین های سطحی در قطعه کامپوزیتی به دو دسته ژل کت (سطح درگیر با قالب) و تاپ کت (بیرونی ترین سطح لایه گذاری شده) دسته بندی می شود.
لایه ژل کت: ضخامتی در حدود 0.5 میلی متر دارا می باشد (وزن واحد سطح در حدود 500 گرم بر مترمریع). با توجه به کاربری قطعه از انواع رزین های پلی استر با خواص خاص در سطح می توان استفاده نمود اما به طور کلی استفاده از رزین پلی استر ایزو به همراه افزودنی های لازم، جهت استفاده در لایه ژل کت پیشنهاد می گردد.
لایه تاپ کت: از حساسیت کمتری به نسبت ژل کت برخوردار می باشد و استفاده از رزین های خاصی که امکان پخت در هوا را دارد، پیشنهاد میگردد.
رزین با نشر استایرن کنترل شده: استایرن اضافه شده در رزین پلی استر، فرار می باشد که از نظر محیط زیست و نیز آلودگی محیط کار یک موضوع مهم و مشکل در صنعت کامپوزیت می باشد که با روش های مختلفی می توان این مشکل را برطرف نمود:
الف) کاهش درصد استایرن
ب) تغییر استایرن با مونومری دیگر که فراریت کمتری دارد
ج) اضافه نمودن مواد فیلم ساز و غیر سازگار با رزین (مواد پارافینی)
پخت (cure) رزین پلی استر:
جهت کنترل پروسه پخت رزین پلی استر (تغییر حالت مایع به جامد و ایجاد ساختار شبکه ای) پارامترهای زیر تاثیرگذار می باشند:
- مقدار شروع کننده (کاتالیزر)
- میزان شتاب دهنده و کاهنده رزین پلی استر و زمان افزودن آن
- دما
- زمان
رزین پلی استر در صورتی که دما در حدود 160 درجه سلسیوس باشد، بدون افزودن هیچ گونه کاتالیزور و شتاب دهنده ای فرآیند پخت و ژل شدن آغاز می گردد، با افزودن کاتالیزر این دما تا حدود 50 درجه سلسیوس کاهش می یابد و با اضافه کردن شتاب دهنده پروسه پخت در دمای محیط 25 درجه سلسیوس قابل انجام می باشد. حال می توان با کنترل هر سه پارامتر ذکر شده، زمان پخت، جهت دستیابی به خواص قطعه کامپوزیتی ایده ال را مدیریت نمود.
در صورت افزایش برآیند پارامترهای ذکر شده، دمای قطعه کامپوزیتی در حین پخت افزایش یافته (امکان افزایش دما تا 170 درجه سلسیوس می باشد) و باعث تغییر رنگ محصول نهایی و ایجاد ترک در قطعه می گردد. در صورت کاهش نیز باعث عدم پخت کامل قطعه و عدم دستیابی به خواص نهایی ایده ال محصول می گردد.
مراحل پخت رزین:
پخت رزین پلی استر شامل سه مرحله می باشد:
1) زمان ژل شدن: فاصله زمانی میان اضافه کردن شتاب دهنده تا زمان ژل شدن رزین
2) زمان سخت شدن: فاصله زمانی میان ژل شدن تا سخت شدن قطعه (خروج قطعه از قالب) سختی سطح در حدود 15 بارکول
3) زمان سخت شدن نهایی: فرآیند پس پخت جهت دست یابی به حداکثر خواص رزین ( سختی سطح در حدود 45 بارکول)
انواع شروع کننده های (کاتالیزر) رزین پلی استر:
متداول ترین کاتالیزرهای مصرفی در صنعت کامپوزیت، از نوع پراکسیدهای آلی می باشند که در بازار ایران به نام اسید (خشک کن) شناخته می شود. این مواد بدلیل واکنش پذیری بالا، به صورت رقیق شده در یک محلول و یا خمیری در بازار عرضه می گردند. میزان مصرف آن 1 الی 3 درصد وزن رزین است و انواع آن به صورت زیر می باشد:
جهت پخت در دمای محیط:
متیل اتیل کتون پراکساید (MEKP): متداول ترین و ارزان ترین شروع کننده می باشد که برای سلامتی مضر است.
ترشری بوتیل پراکساید (TBP)
سیکلو هگزانون پراکساید (CHP): جمع شدگی کمتر، پیک دمایی کمتر و برای قطعات ضخیم و حجیم مناسب می باشد.
استیل استن پراکساید (AAP): زمان پخت (پیک دما را افزایش می دهد) را کاهش می دهد و برای قطعات نازک و ظریف مناسب می باشد.
جهت پخت در دمای بالا (حرارتی) همانند روش پالتروژن:
بنروییل پراکساید(BPO): جهت پخت دمای حدودی 100 تا 140 درجه سلسیوس نیاز می باشد و با توجه به ابعاد، حجم قطعه، دما و نوع رزین مدت زمانی در حدود 1 الی 10 دقیقه نیز صرف پخت قطعه می گردد. (بدون نیاز به شتاب دهنده)
شتاب دهنده رزین پلی استر:
به طور معمول شتاب دهنده ها قبل از استفاده رزین، به آن افزوده می شوند و در بعضی مواقع رزین مخلوط شده با شتاب دهنده، به بازار عرضه می گردد که در این صورت با اضافه کردن صرفا شروع کننده، واکنش پخت رزین آغاز می گردد. درصد افزودن شتاب دهنده به رزین مقدار حداقلی به میزان 0.1-0.5 درصد وزنی رزین می باشد.
انواع شتاب دهنده ها:
نمک های آلی کبالت (همانند نفتانات کبالت یا اکتیوات کبالت): به صورت رقیق شده و رنگ بنفش و بی رنگ در بازار موجود می باشد.
آمین های نوع سوم (همانند دی متیل آنیلین یا دی اتیل آنیلین): این شتاب دهنده از نوع کبالت فعال تر می باشد.
توجه 1: درصد شروع کننده ثابت و جهت تغییر در مدت زمان پخت صرفا تغییر درصد شتاب دهنده مد نظر قرار گیرد
توجه 2: هیچگاه شروع کننده و کبالت مجزا با یکدیگر مخلوط نشوند ( واکنش این دو ماده با یکدیگر انفجاری می باشد)
توجه 3) پیشنهاد می گردد دمای محیط کارگاه ساخت قطعه کامپوزیتی زیر 15 درجه سلسیوس نباشد.
وینیل استر:
رزین های وینیل استر حد واسط رزین های پلی استر و اپوکسی می باشند (در بعضی منابع علمی رزین وینیل استر را زیر مجموعه انواع رزین های پلی استر قرار می دهند) کاربری اصلی رزین های وینیل استر بیشتر در ساخت قطعات مقاوم در برابر مواد شیمایی همانند لوله ها و مخازن می باشد.
ویژگی ها:
مقاومت شیمیایی بالاتر از پلی استرها و قابل استفاده در محیط های شیمیایی خاص (مقاوم در برابر خوردگی اسید و باز)
مقاومت مکانیکی مطلوب (در حین اعمال نیروی کششی، ازدیاد طول بالاتری دارد و منعطف تر از رزین های پلی استر می باشد. چفرمگی (سفتی) بالاتری از پلی استرها دارد)
دمای تغییر شکل حرارت (HDT) بالاتر از رزین های پلی استر
آغشتگی و چسبندگی مناسب با الیاف
جذب آب کم بعد از تولید قطعه کامپوزیتی
مقاوم در برابر نور فرابنفش
سرعت پخت آرامتر از پلی استر
جمع شدگی قطعه بعد از تولید کمتر از پلی استر می باشد.
قیمت دو تا پنج برابر رزین پلی استر.
منبع: شیمی افسون